An das Material, aus dem Feuerräume von Öfen und Kaminen gebaut sind, werden hohe Ansprüche gestellt. Vor allem muss es extrem hitzebeständig sein und im oberen Teil Temperaturen von über 1200 Grad standhalten, ohne zu reißen, sich zu verformen oder anderweitig Schaden zu nehmen. Auch eine chemische Beständigkeit (unter anderem gegen Säuren) ist gefordert. Und drittens werden Feuerraummaterialien auch mechanisch beansprucht, denn nicht jeder ist beim Asche auskehren oder Nachlegen von Holz zimperlich mit der Feuerraumauskleidung. Das ist dann auch schon der kleinste gemeinsame Nenner, der für die Feuerraummaterialien gilt. Sie können im übrigen stark voneinander abweichende Eigenschaften haben, die ihre Verwendbarkeit für ganz unterschiedliche Ofentypen begründet.
Die häufigsten Feuerraummaterialien sind zweifellos Schamotte und Vermiculit, gefolgt von Gusseisen Feuerbeton. Naturstein und Kalziumsilikat spielen bei der Innenauskleidung von Ofen- und Kamin-Brennräumen nicht die dominierende Rolle, weil sie nur von einzelnen Anbietern auf den Markt gebracht wurden. Bei Kalziumsilikat, das an anderer Stelle im Ofenbau ein seit vielen Jahren bewährter Baustoff ist, liegt das daran, dass es als Produkt für die Verwendung im Feuerraum erst seit kurzem verfügbar ist. Ein weiteres, exklusives Feuerraum-Material ist keramische Schamotte „Keramott“ von Austroflamm, der eine spezielle Rezeptur zugrunde liegt, die den Feuerraum nicht nur sauber aussehen, sondern auch sauber halten lässt, denn es lässt sich dank glatter Oberfläche gut reinigen.
Schamotte
Schamotte ist das wichtigste Material für den individuellen handwerklichen Ofenbau, während Vermiculit vor allem im industriellen Ofenbau – und da vor allem für Kamine und Kaminöfen – verwendet wird. Mehr dazu im nächsten Absatz. Hier ist nur hervorzugeben, dass Schamotte und Vermiculit beinahe entgegengesetzte physikalische Eigenschaften haben. Während Vermiculit in erster Linie eine Wärme dämmende Wirkung hat, weist Schamotte eine besondere Wärmespeicherfähigkeit auf. Deshalb und wegen seiner hohen Temperaturwechselbeständigkeit ist Schamotte das ideale Material für Grundöfen oder auch für Kombiöfen. Das Material kommt hier sowohl beim Brennraum selbst als auch bei nachgeschalteten Zugsystemen zur Verwendung. Da es in den Zügen nicht so großer thermischer Belastung ausgesetzt ist, können dafür auch einfachere Schamottequalitäten verwendet werden.
Schamotte ist ein gesteinsähnliches, künstlich hergestelltes, feuerfestes Material mit 10 bis 45 Prozent Aluminiumoxid-Anteil (Al2O3). Sie ist der Klassiker unter den Feuerraum-Materialien und wird seit Jahrhunderten im Ofenbau eingesetzt. Man unterscheidet Schamotte mit einem höheren Quarzanteil und einem Al2O3-Gehalt zwischen 10 und 30 Prozent (saure Schamotte) und Normalschamotte mit einem Al2O3-Gehalt zwischen 30 und 45 Prozent. Rohstoff für das Endprodukt im Ofenbau sind Schamotte und Ton, wobei der Rohton sowohl zur Bindung der Schamottekörnung als auch zur Ergänzung des Gefüges eingesetzt wird.
Ofenschamotte wird wie folgt hergestellt: Nach einem Vorbrand des Tons wird dieser mechanisch zerkleinert (gebrochen oder gemahlen). Für die Verwendung im Ofenbau wird Schamotte mit möglichst reinem Rohton benötigt. Bei schlechteren Qualitäten kann ein relativ großer Quarzanteil im Rohstoff enthalten sein (saure Schamotte). Ebenso ist es von Vorteil, einen möglichst hohen Kaolinitanteil im Ton zu haben, da dieser keine Alkalien mitbringt. Ein Schamottestein aus reinem Ton hätte eine enorme Brennschwindung. Durch das Vorbrennen wird ein Großteil der Schwindung vorweggenommen, so dass der Stein weniger rissanfällig wird. Nach dem Zerkleinern und Fraktionieren in unterschiedliche Körnungsgrößen wird die Schamotte im Schlickerguss-Verfahren oder durch Strang- beziehungsweise Trockenpressen geformt. Ein trockengepresster Stein weist dabei bessere feuerfeste Eigenschaften auf als die unter höherer Wasserzugabe plastisch geformten oder schlickergegossenen Steine. Allerdings lassen sich nicht alle gewünschten Formvarianten im Trockenpressverfahren herstellen.
Die Verarbeitung beim Ofenbau erfolgt unter Verwendung spezieller Schamottemörtel, die je nach Anwendungszweck ebenfalls in einer Vielzahl unterschiedlicher Qualitäten und Mischungen erhältlich sind. Bei erfahrenen Ofenbauern haben sich im Laufe der Jahre meist individuelle Vorlieben für bestimmte Mörtel und auch Schamottequalitäten entwickelt.
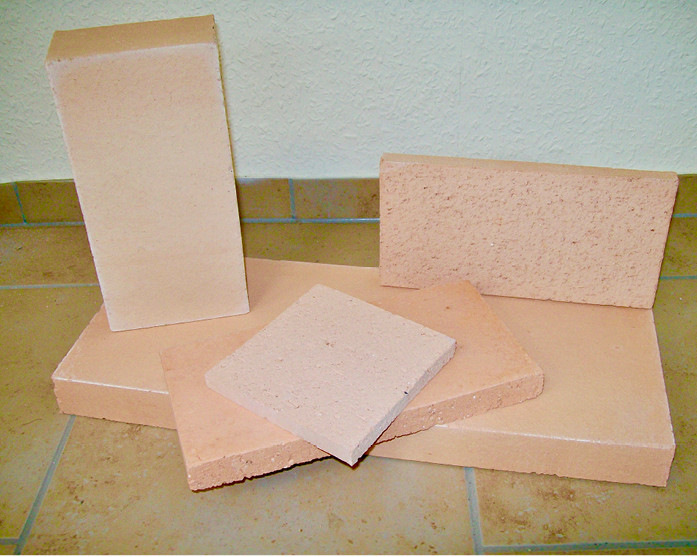
Foto: Radeburger
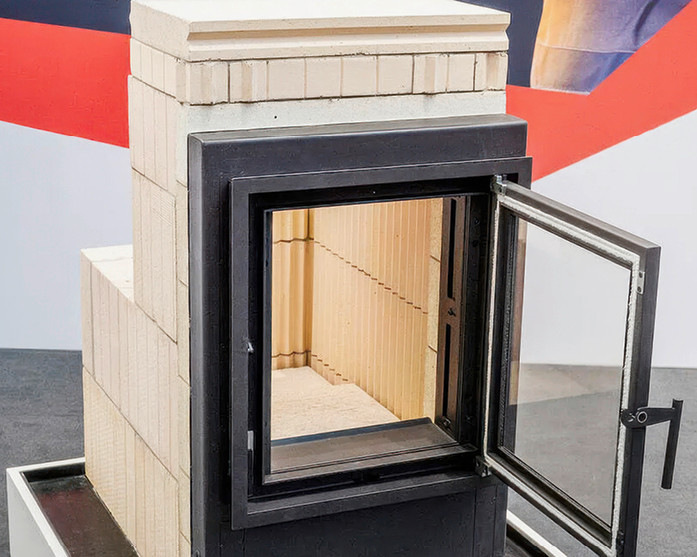
Foto: Rath
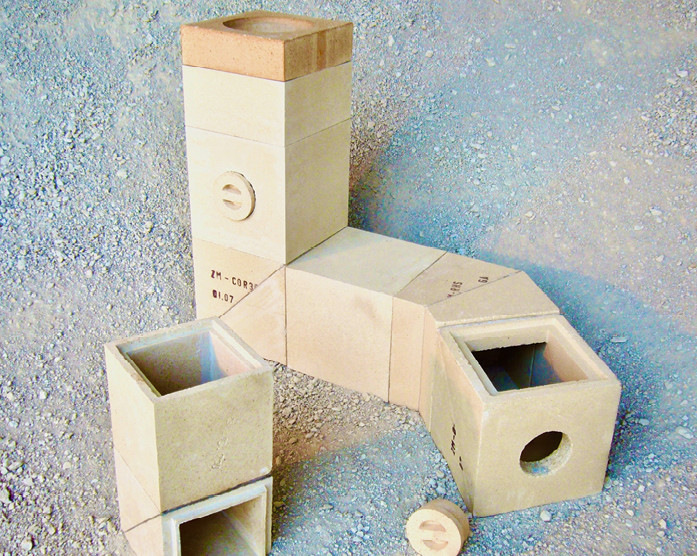
Foto: Rath
Vermiculit
Seit über 40 Jahren wird im modernen Ofenbau Vermiculit für Feuerraumauskleidungen verwendet, und zwar sowohl im industriellen Bereich (bei der Kaminofen- und Kamin- beziehungsweise Heizensatz-Herstellung), aber auch im individuellen Ofenbau. Vermiculit ist ein ökologischer Naturbaustoff aus der Familie der Glimmer. Der Rohstoff wird in Minen (meist in Südafrika) abgebaut. Außer im Ofenbau wird Vermiculit noch für zahlreiche weitere Zwecke verwendet, zum Beispiel im baulichen Brandschutz. Es kommt es in der Verpackungstechnik für Medizinprodukte ebenso zum Einsatz wie zur Bodenverbesserung in der Landwirtschaft, ja, es dient sogar als Futtermittelzusatz, was die ökologische Unbedenklichkeit belegt.
Mit seiner Wärme dämmenden statt speichernden Eigenschaft weist Vermiculit ein komplett anderes Einsatzprofil als Schamotte auf. Die Dämmwirkung führt zu höheren Temperaturen im Brennraum, was durch eine vollständigere Verbrennung zu einer verringerten Emissionsbelastung im Abgas beiträgt. Insbesondere bei modernen Warmluftöfen wird mit Vermiculit eine rasche Wärmeentwicklung im Aufstellraum erzielt. Durch die heute üblichen großen Kamin-Sichtscheiben wird außerdem mehr Strahlungswärme abgegeben. Das kann, muss aber nicht zwangsläufig ein Vorzug sein, denn es kann ein Überheizen des Aufstellraums begünstigen, andererseits sorgen die höheren Temperaturen eben auch für eine verringerte Verschmutzungsneigung der Sichtscheiben.
Für die Verwendung als Baustoff muss Vermiculit zunächst thermisch aufbereitet werden. Beim raschen Erhitzen auf ca. 1.000 °C verdampft das im Rohvermiculit gebundene Wasser explosionsartig, so dass die Glimmerschichten voneinander abgehoben (exfoliert) werden. Dadurch entsteht eine fächerartige Struktur mit großen Hohlräumen und großer Oberfläche. Derart aufbereitet ist Vermiculit zur Weiterverarbeitung für die vielseitigsten Anwendungsmöglichkeiten geeignet.
Für die meisten Einsatzgebiete wird Vermiculit anschließend zu einem Plattenwerkstoff geformt, der in seiner äußeren Erscheinung oft Pressholzplatten ähnelt und sich auch mit den für die Holzbearbeitung gebräuchlichen Werkzeugen verarbeiten lässt. Ein großer Vorzug beispielsweise gegenüber Gipskartonplatten ist, dass dabei so gut wie kein Staub entsteht. Die Weiterverarbeitung ist deshalb ein außerordentlich sauberer Vorgang, der weder die Gesundheit des Handwerkers beeinträchtigt, noch die Baustelle verschmutzt. Vermiculitplatten werden für verschiedene Aufgaben in unterschiedlichen Stärken und Abmessungen hergestellt.
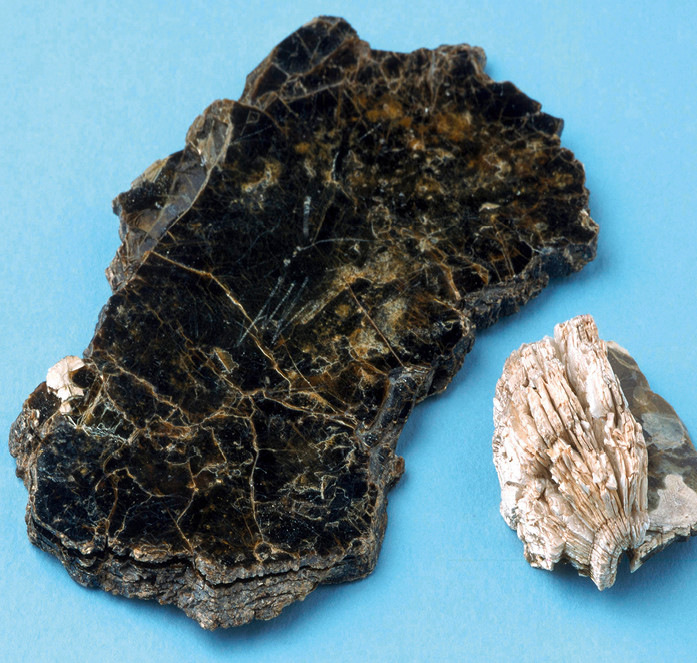
Foto: Technophsik
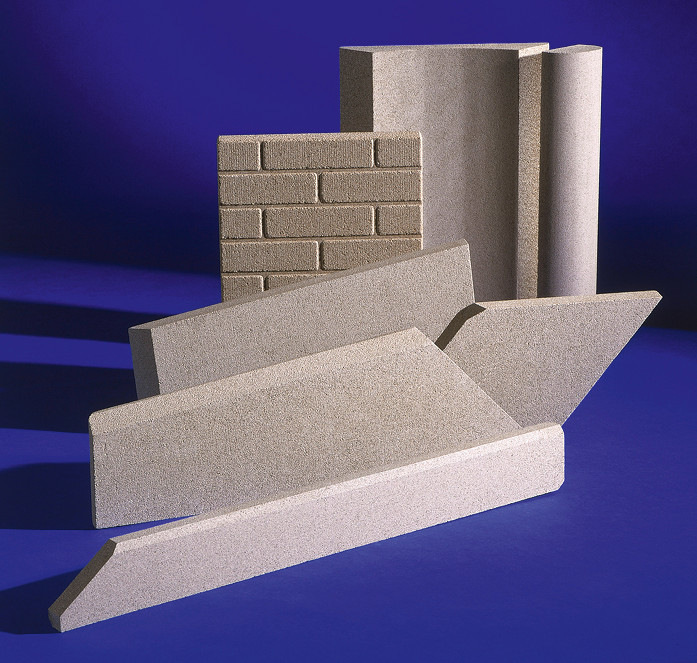
Foto: Technophysik
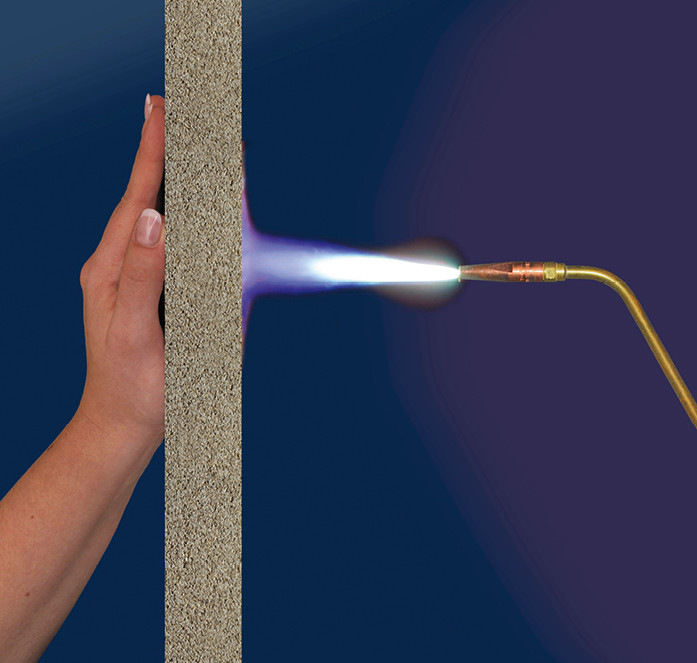
Foto: Technophysik
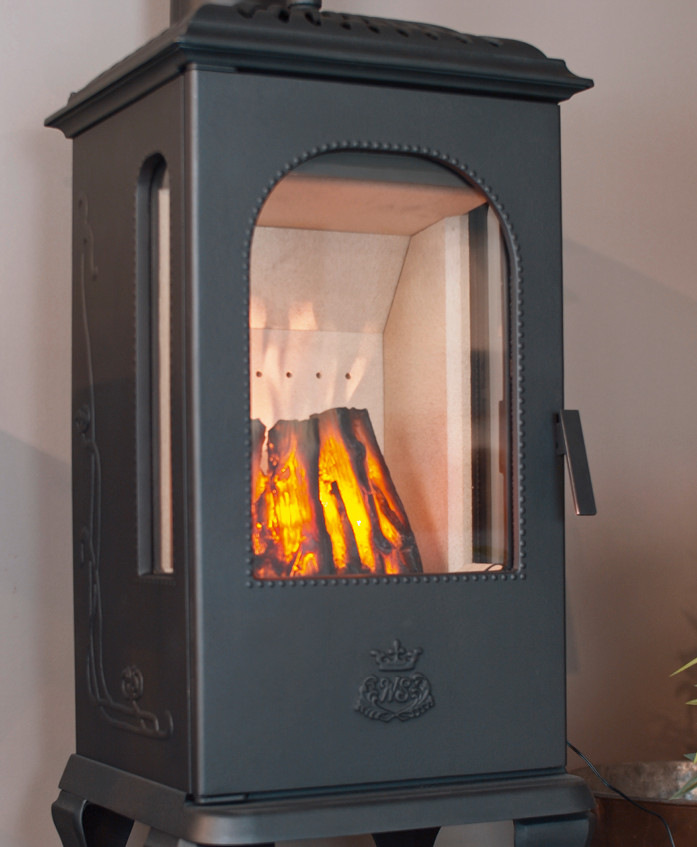
Foto: Westbo
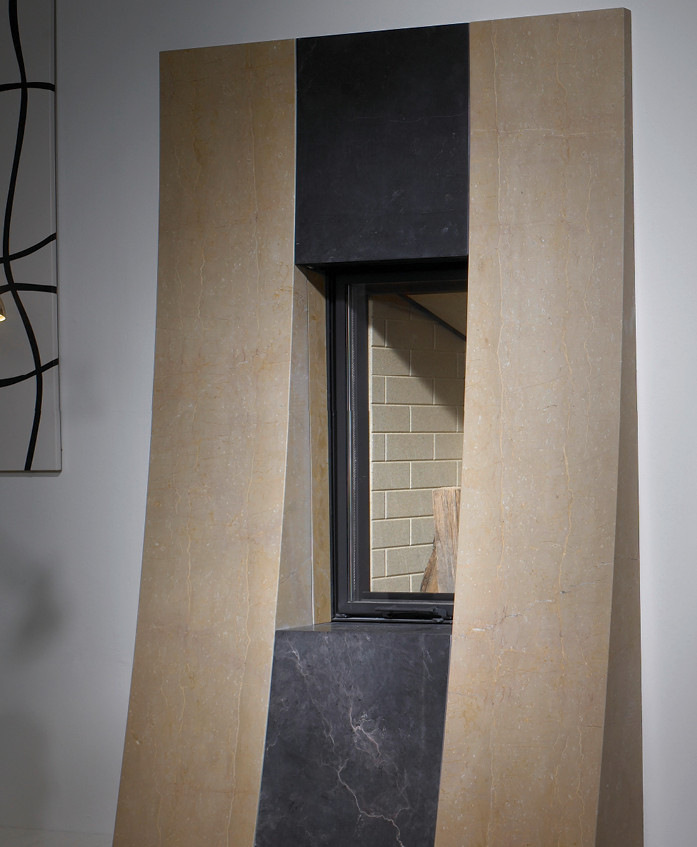
Foto: Camina
Gusseisen
Reine Feuerräume aus Gusseisen gab es bei historischen Öfen häufiger. Bei neueren Einzelraumfeuerstätten sind sie eine Ausnahme. Am Verbreitesten sind sie noch bei italienischen Herden und Öfen, aber auch einige Ofenmodelle aus deutscher und skandinavischer Produktion werden nach wie vor als reine Gussöfen ohne Fremdmaterialien gefertigt. Die meisten Hersteller von Gussöfen und gusseisernen Heizeinsätzen kleiden diese jedoch zumindest teilweise mit Schamotte oder Vermiculit aus, je nachdem, wie diese Brennkammern eingesetzt werden sollen. Die äußere Gusseisenhülle solcher Heizeinsätze hat einige entscheidende Vorzüge zu bieten: Gusseisen ist ein hervorragender Wärmeleiter, es ist auch unter hoher Temperaturbeanspruchung extrem formstabil und weist eine hohe Korrosionsresistenz auf. Durch seine große Dichte kann Gusseisen bei entsprechender Masse selbst Wärme speichern. Sorgfältig konstruierte und gefertigte Gussöfen sind sehr langlebig und können mehrere Generationen halten.
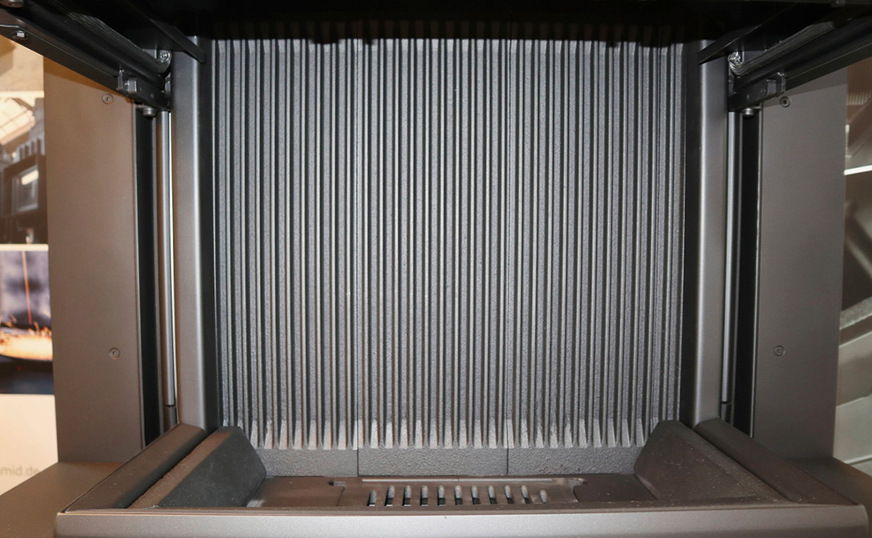
Foto: Martin Henze
Feuerbeton
Feuerbeton gibt es entweder als Formsteine oder als Sackware, um selbst einen Ofen vor Ort zu bauen. Das Material ist besonders hart und temperaturwechselbeständig, andererseits gibt es nur wenige Hersteller, die ihre Feuerräume damit ausstatten. Einer von ihnen ist Ortner. Ihr Grundofenstein aus Feuerbeton bildet das Fundament für ihre Speicherfeuerstätten. Diese Feuerräume bilden gemeinsam mit dem Hochleistungsspeicher „KMS“ die Ortner Speicheröfen 2.0. Die besonderen Materialeigenschaften von Ortner Feuerbeton führen in Verbindung mit der optimalen Zuluftführung zu höchsten Feuerraumtemperaturen und fast rückstandsloser Verbrennung.
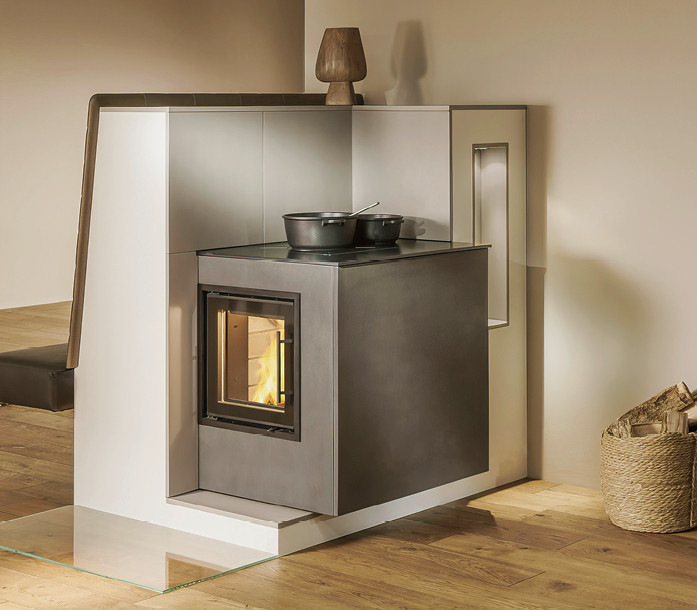
Foto: Ortner
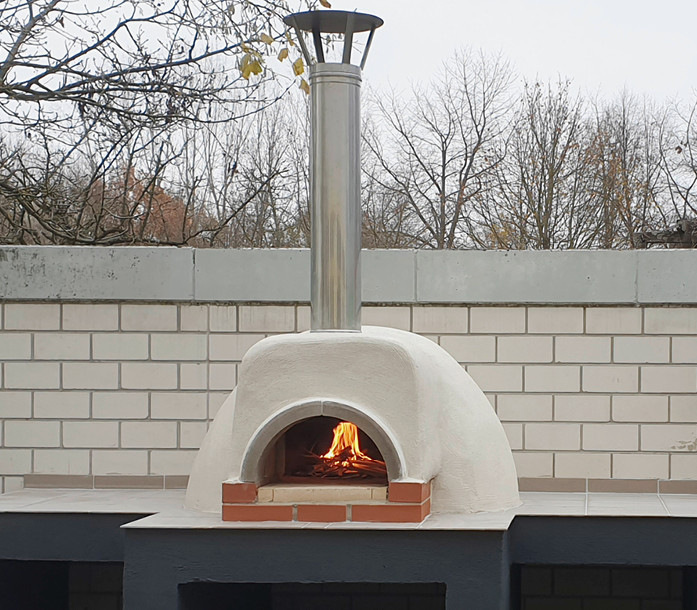
Foto: Wolfshöher Tonwerke
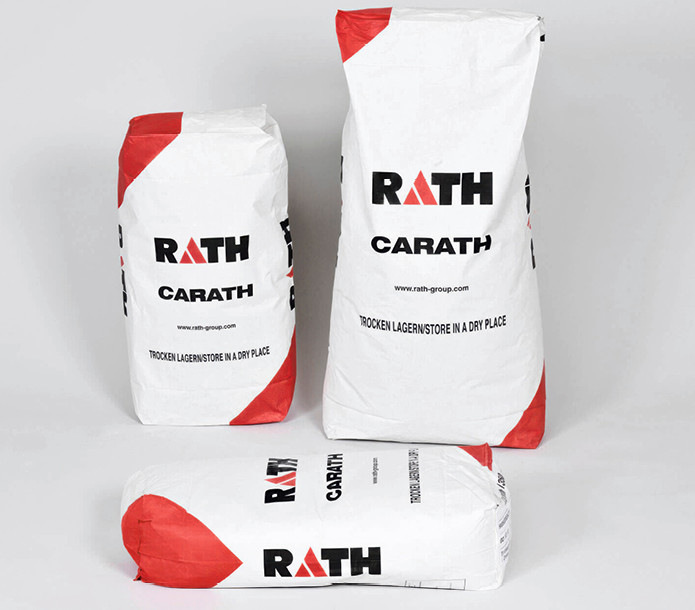
Foto: Rath
Kalziumsilikat
Mit der Feuerraumplatte „Silcapan 750FB“ bietet Silca die einzige Calciumsilikatplatte für den direkten Einsatz im Feuerraum. Die Platte besteht aus natürlichen Rohstoffen ohne zugesetzte Bindemittel. Die helle reflektierende Oberfläche und die guten Dämmeigenschaften ermöglichen ein schnelles Erreichen der stationären Temperatur im Feuerraum. Alternativ ist „Silcapan 750F“ auch in einer dunklen Ausführung erhältlich. Außer durch die hervorragenden Dämmeigenschaften überzeugt die Feuerraumplatte mit einer hohen Druck- und Biegefestigkeit. Die Feuchteunempfindlichkeit gegenüber Kondensat und hoher Luftfeuchtigkeit ist ein weiterer großer Vorteil. Die innovative Feuerraumplatte trägt durch ihre Eigenschaften zur Reduzierung von Emissionen bei. „Silcapan 750FB“ wird als Austauschplatte in Standardformaten vom gut aufgestellten Großhandel angeboten. Silca bietet Feuerstättenherstellern auch speziell auf ihre industrielle Verarbeitung zugeschnittete Feuerraumelemente aus diesem Material.
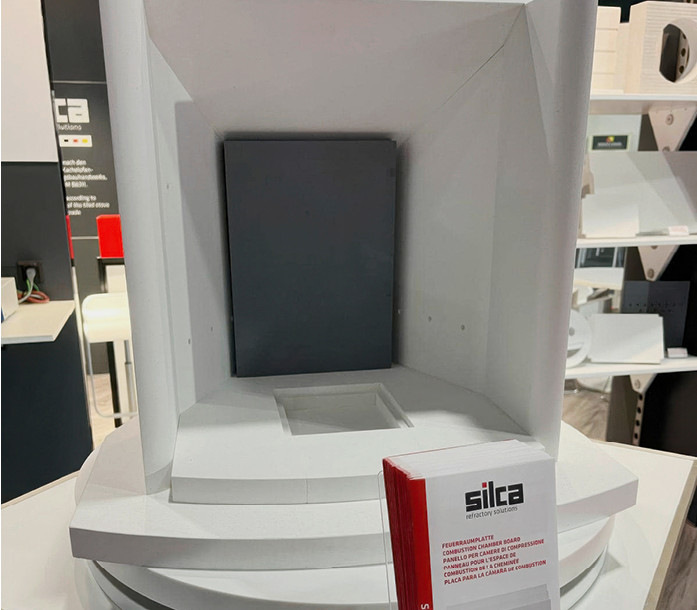
Foto: Silca
Naturstein
Normalerweise ist Naturstein aus wärmephysikalischen Gründen nicht für den direkten Einsatz im Feuerraum geeignet, denn in der Regel ist hier nicht die notwendige Temperaturwechselbeständigkeit und eine homogene Wärmeleitfähigkeit gegeben. Der hochwertige Mammuti-Speckstein, der für die massiven Specksteinöfen des finnischen Herstellers NunnaUuni genutzt wird, bildet hier aber eine Ausnahme. Von speziell geschulten Mitarbeitern des Herstellers werden ausgewählte Specksteinelemente ausgesucht und diese können unmittelbar auch im Feuerraum eingesetzt werden, was zu einer hohen Speicherfähigkeit führt.
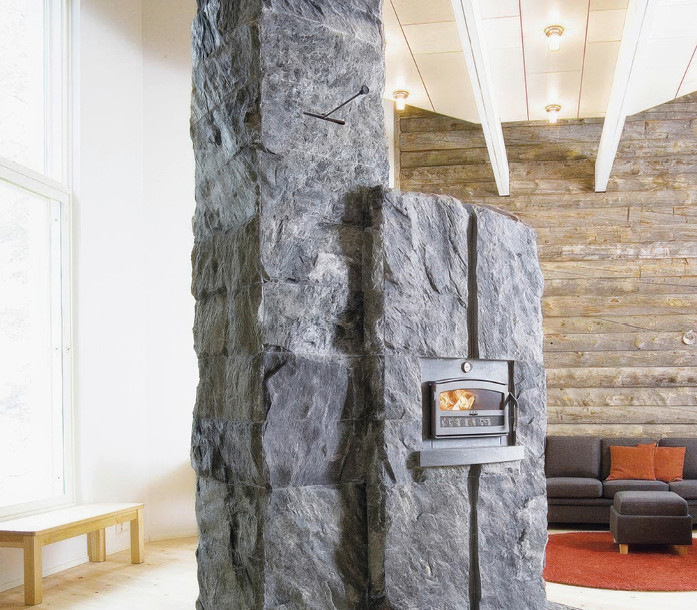
Foto: NunnaUuni

Foto: Wolfshöher Tonwerke
Stationen der Schamotteherstellung
Ein typischer Transportkosten senkende Standort für die Schamotteproduktion ist das Werk von Wolfshöher Tonwerke in Neunkirchen am Sand, denn es liegt wenige hundert Meter von der Tongrube entfernt, aus der das Rohmaterial für die Schamotteplatten gewonnen wird. Exemplarisch zeigen wir hier ein paar Stationen der Schamotteherstellung im Bild.